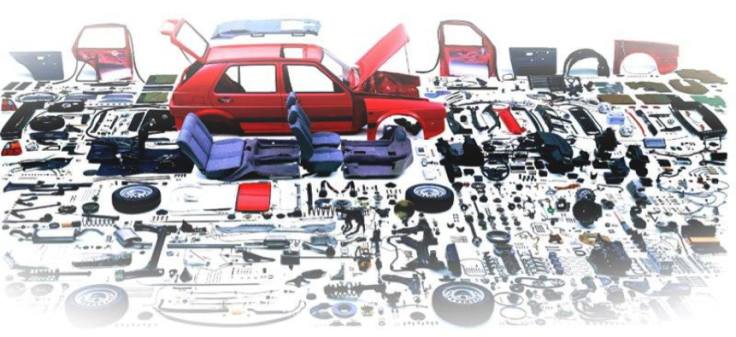
Today, automotive plastics play an important role in the automotive industries. The market of automotive plastics now is driven by the increasing demand on automobiles which favor the trend of low emissions, light weight, and improved designs. For a time, the automotive market has been experiencing a trend of reduced vehicle weight to improve fuel efficiency. The demand of plastic in the automotive industry is rising because automotive plastic parts ensure considerable weight reduction
A 10% reduction in auto weight can save more than 5% to 7% of fuel, which help to lower the level of carbon dioxide emissions over the service life of the autos. At the same time, the overall performance of autos in terms of handling and acceleration has also been significantly improved. The weight reduction at the unbalance point is good for vibration and noise reduction. In addition to reducing vehicle weight, automotive plastics can enhance the aesthetics of the vehicle, reduce vibration and noise and improve cabin insulation.
Therefore, plastic automotive prototype as the previous manufacturing step is also attached great attention in the automotive industry. This article from WayKen Rapid Manufacturing as following will introduce the technologies for plastic automotive prototype and the applications of plastic in Automotive Industry.
Technologies for Plastic Automotive Prototype
1) CNC Machining for Plastic Automotive Prototype
CNC prototyping is an optimal option for one-off custom parts and is available in machining virtually any block material directly according to 3D CAD data. WayKen offers advanced CNC machining services for auto prototypes, including CNC milling, CNC turning, drilling and tapping for various automotive plastics, such as ABS, PMMA, PC, etc..
2) Urethane Vacuum Casting for Plastic Automotive Prototype
Vacuum casting (known as polyurethane casting also) can be used to closely simulate to final injection molded parts or finished products. Generally, molds are made from silicone rubber and the master pattern will be manufactured by CNC Machining or SLA 3D Printing. These molds can cast automotive plastic parts same as the master pattern regarding to details and textures and give consistent finishes from one part to the next. The production-like parts can be achieved by vacuum casting, including mechanical properties, colors, and finishes.
3) 3D Printing --SLA & SLS For Plastic Automotive Prototype
Rapid prototyping for automotive plastic parts with 3D printing is a quick, easy and cost-effective way to turn great ideas into successful products. These printed automotive plastic parts can not only help verify a design, but also express an idea issues early in the development process and give feedback directly on design fix, preventing costly changes to the hard tool when the product is in full production.
4) Rapid Injection Molding for Low Volume Production of Automotive Plastics
Rapid injection molding is one of plastic molding, which can not only manufacture hundreds of pilot-run production for test prototypes to confirm the final product, but also provide on-demand production of end-use parts for low-volume manufacturing. At WayKen, We combined traditional injection mold tooling with rapid mold tooling to produce plastic automotive parts quickly and cost-efficiently regarding to production quality instead of molded prototypes still in development and testing phases.
Applications of Automotive Plastics
Generally, automotive plastics include Polycarbonate, Polyurethane, Acrylonitrile Butadiene Styrene (ABS), Polyvinyl Chloride (PVC), Polypropylene, Polyethylene, Polymethyl Methacrylate (PMMA), and Polyamide. Among them, three types of auto plastics make up approximately nearly 66% in total automotive plastics used: polypropylene (32%), polyurethane (17%) and PVC (16%).
1) Polypropylene (PP)
Polypropylene (thermoplastic polymers) is used in a wide variety of applications in interior and exterior car parts, such as car bumpers, chemical tanks, cable insulation, gas cans, carpet fibers, etc.
2) Acrylic (PMMA)
PMMA is a Transparent thermoplastic, which is typically used as a lightweight or shatterproof glass substitute in windows, lighting parts, displays, and screens. The excellent transparency of PMMA make itself become the first choice of automotive lenses, especially for automotive prototypes, widely used in the automotive prototyping industry,
3) Polyurethane (PU)
Solid Polyurethanes (elastomeric materials) have excellent properties such as toughness, flexibility, abrasion resistance and temperature resistance, which are commonly used in flexible foam seats, foam insulation boards, elastic wheels and tires, automotive suspension bushings, cushions, electrical potting compounds, hard plastic parts
4) Acrylonitrile Butadiene Styrene (ABS)
Acrylonitrile Butadiene Styrene (copolymer) is made from polymerizing styrene and acrylonitrile in the presence of polybutadiene. Styrene gives the plastic a glossy, impervious surface. Butadiene is a rubbery substance that provides resilience even at low temperatures. It is commonly used in body parts, instrument panels, wheel covers.
5) PolyVinyl-Chloride (PVC)
The advantage of PVC is good flexibility, flame retardancy, good thermal stability, high gloss and low lead content. PVC is commonly used in car dashboards, cable jackets, pipes, doors.
6) Polystyrene (PS)
Polystyrene is naturally clear, which is commonly used in equipment housings, buttons, auto fittings, monitor bases.
7) Polyamide (PA, Nylon 6/6, Nylon 6)
Nylon 6/6 is often used when a low cost, high mechanical strength, rigidity and stability are required, commonly used for gears, bushings, cams, bearings, weatherproof coatings.
8) POM (Polyoxymethylene)
POM has excellent stiffness and yield strength, which is suitable for interiors and exteriors aesthetic automotive plastic parts, fuel systems and pinions.
9) Polyethylene (PE)
Polyethylene has high impact resistance, low density and toughness, commonly used in car body (glass reinforced) and is good for electrical insulation.
10) Polycarbonate (PC)
Amorphous polycarbonate polymers have a unique combination of stiffness, hardness and toughness. The common PC includes White PC and Black PC, which widely used in bumpers, automotive lighting parts. Its strength is higher than PMMA while not as clear as PMMA.
11) Polyethylene Terephthalate (PET)
PET is usually used in the manufacture of synthetic fibers and plastic bottles. Regarding to automotive plastic parts, it can be used in wiper arm and gearbox, headlamp holder, engine cover, connector housing.
12) ASA (acrylonitrile styrene acrylate)
ASA has high toughness and rigidity, good chemical and thermal stability, excellent resistance to weather, aging and yellowing, and high gloss. It is widely used in automotive light housing profiles, interior parts and outdoor applications.
Concluding Remarks
With the increasing demands of Automotive Plastics, critical manufacturing technologies for various applicable plastics are attached more and more importance by automotive parts manufacturers. Wayken is dedicated to develop its technology in manufacturing automotive plastic parts, from the machining precision to surface finishing for varied Automotive Plastics, becoming stronger in auto plastics manufacturing.